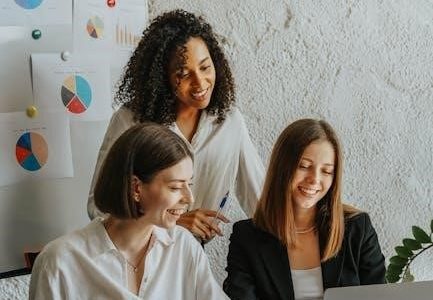
unc thread chart pdf
The UNC thread chart, based on ANSI B1.1, provides standardized specifications for fastener dimensions, ensuring compatibility and reliability in engineering applications. It outlines nominal diameters, threads per inch, major diameters, and pitches, serving as a crucial reference for manufacturers and designers to ensure precise thread cutting.
Overview of UNC Thread Standard
The UNC thread standard, defined by ANSI B1.1, establishes uniform specifications for screw threads, ensuring compatibility and reliability across engineering applications. It specifies nominal diameters, threads per inch, major diameters, and pitches, providing a consistent framework for manufacturers and designers. The standard is widely used in industries like automotive and aerospace, where precise thread dimensions are critical for assembly and performance. By adhering to UNC standards, professionals can maintain interchangeability and minimize errors in fastener applications, contributing to the overall quality and safety of mechanical systems.
Importance of Thread Charts in Engineering
Thread charts, such as the UNC thread chart, are essential tools in engineering, providing standardized screw thread specifications that ensure precision and compatibility. They help prevent dimensional errors, enabling accurate mating of parts and maintaining structural integrity. By adhering to these charts, engineers can select appropriate tools and materials, streamline manufacturing processes, and reduce production costs. The charts also facilitate compliance with industry standards like ANSI B1.1, ensuring reliability and safety in applications across automotive, aerospace, and industrial machinery. Their widespread use underscores their critical role in maintaining quality and consistency in modern engineering practices.
UNC Thread Specifications
UNC thread specifications, outlined in ANSI B1.1, detail nominal diameters, threads per inch, major diameters, and pitch dimensions, ensuring precise manufacturing and compatibility across applications.
Nominal Diameter and Threads per Inch
Nominal diameter refers to the major diameter of the thread, while threads per inch (TPI) indicate the number of threads along a one-inch length. The UNC standard specifies these values for each fastener size, ensuring compatibility and proper fitment. For example, a 1/2-inch UNC thread has a nominal diameter of 0.500 inches and 13 TPI. These measurements are critical for selecting the correct tools, such as taps and dies, and for ensuring that components mate correctly. The chart provides a comprehensive list of sizes, making it an essential reference for engineers and manufacturers.
Major Diameter and Pitch Dimensions
The major diameter is the largest diameter of the thread, while the pitch is the distance between corresponding points on adjacent threads. In the UNC standard, these dimensions are precisely specified for each thread size. For example, a 1/2-inch UNC thread has a major diameter of 0.500 inches and a pitch of 1/13 inch. These measurements ensure proper fitment and load distribution. The chart provides these dimensions in both inches and millimeters for international compatibility. Accurate knowledge of these values is essential for engineers to design and manufacture components that meet UNC standards, ensuring safety and reliability in fastened joints.
Tolerances and Allowances
Tolerances and allowances are critical in ensuring proper thread fitment and functionality. The UNC thread chart specifies maximum material condition (MMC) and fundamental deviations for threads. Tolerances define acceptable limits for major and minor diameters, pitch, and other dimensions. Allowances, such as the minimum clearance between mating threads, prevent over-tightening. These specifications ensure parts are interchangeable and meet ANSI B1.1 standards. Engineers use these guidelines to avoid oversizing or undersizing threads, which could lead to assembly issues or reduced strength. Proper application of tolerances and allowances ensures reliability and safety in fastened joints, making them essential for precise manufacturing and design processes.
Applications of UNC Threads
UNC threads are widely used in automotive, aerospace, and industrial machinery for reliable fastening solutions. Their standardized dimensions ensure compatibility and strength across various engineering applications.
Use in Automotive Industry
UNC threads are integral to the automotive industry, ensuring durable and precise fastening solutions for vehicles. They are used in engine components, chassis parts, and assemblies, where reliability is critical. The standardization of UNC threads simplifies manufacturing processes and guarantees interchangeability. With a focus on strength and resistance to wear, these threads are essential for withstanding the stresses of automotive applications. Their widespread adoption ensures compatibility across different vehicle models and components, making them a cornerstone of automotive engineering and design.
Role in Aerospace Engineering
UNC threads play a pivotal role in aerospace engineering, where precision, durability, and weight optimization are critical. These standardized threads ensure compatibility and reliability in aircraft and spacecraft components, such as engine mounts, fasteners, and structural assemblies. The uniformity of UNC threads facilitates easier assembly and maintenance, while their strength and resistance to fatigue are essential for withstanding the extreme conditions of flight. Aerospace applications often require lightweight yet robust materials, and UNC threads are adapted to work seamlessly with these specialized alloys. Their use in modular systems also enhances scalability and integration across different aerospace projects, contributing to the overall efficiency and safety of aircraft design.
Industrial Machinery and Equipment
UNC threads are widely used in industrial machinery and equipment due to their durability and compatibility. They ensure secure connections in pumps, gears, and heavy-duty mechanisms, where high torque and load-bearing capacities are essential. The standardized nature of UNC threads simplifies the assembly and maintenance of large-scale machinery, reducing downtime. They are also integral to hydraulic systems, where precision and sealing are critical. Additionally, UNC threads facilitate the integration of interchangeable parts across different manufacturers, promoting efficiency and cost-effectiveness in industrial operations. Their reliability in harsh environments makes them a cornerstone in the design and functionality of modern industrial equipment, supporting productivity and operational excellence.
Reading the UNC Thread Chart
Understanding the UNC thread chart begins with identifying nominal diameters, threads per inch, and major/minor diameters. It guides selecting taps, dies, and drills for precise thread cutting, ensuring ANSI B1.1 compliance and quality assurance in manufacturing processes across industries.
Understanding Nominal Diameter
Nominal diameter refers to the basic size of the screw thread, typically measured across the thread’s outer edge. It serves as the primary identifier for thread size, ensuring compatibility across components. On the UNC thread chart, nominal diameters are listed alongside threads per inch (TPI), major diameters, and pitches. This information is crucial for selecting appropriate taps, dies, and drills. For example, a 1/2-13 UNC thread has a nominal diameter of 0.5 inches and 13 threads per inch. Accurate interpretation ensures proper fitment and functionality in engineering applications, adhering to ANSI B1.1 standards for quality and reliability.
Interpreting Threads per Inch
Threads per inch (TPI) indicates the density of threads along a screw’s length, measured as the number of threads within a one-inch span. On the UNC thread chart, TPI is paired with nominal diameters to define thread coarseness or fineness. For example, a 1/2-13 UNC thread has 13 threads per inch, while a 1/2-20 UNC thread has 20 threads per inch. Higher TPI values correspond to finer threads, offering increased strength in softer materials but requiring more precise alignment. This measurement is critical for selecting appropriate tools and ensuring compatibility, as it directly impacts the screw’s performance and fitment in various engineering applications.
Major and Minor Diameter Measurements
The UNC thread chart specifies the major and minor diameters for each thread size, ensuring precise fitment and functionality. The major diameter is the largest diameter of the thread, while the minor diameter is the smallest, measured at the base of the thread. These measurements are critical for ensuring proper mating of screws and bolts, as deviations can lead to assembly issues. Tolerances for these diameters are strictly defined to maintain interchangeability and reliability. The chart provides clear values for both diameters, allowing engineers to select components that meet specific design requirements, ensuring optimal performance and durability in various applications.
Selection of Tools for UNC Threads
Choosing the right tools for UNC threads involves selecting appropriate taps, dies, and drill bits to ensure precise thread cutting. The UNC chart guides tool selection for optimal results.
Taps and Dies for UNC Threads
Taps and dies are essential tools for creating UNC threads, ensuring precise thread form and dimensions. Taps are used to cut internal threads in materials, while dies produce external threads on rods or bolts. Both must be selected based on the UNC chart specifications to match the desired thread size and pitch. High-quality taps and dies are crucial for maintaining thread accuracy and preventing damage to the workpiece. Proper maintenance, such as regular cleaning and lubrication, extends tool life. Using the correct tap drill size, as specified in the UNC chart, ensures optimal threading results and minimizes the risk of thread errors or tool breakage.
Drill Sizes for Tapping
Drill sizes for tapping are critical to ensure proper thread formation and integrity. The UNC thread chart specifies the exact drill diameter required for each thread size, guaranteeing a precise fit. Using the correct drill size prevents over- or under-tapping, which can lead to thread inaccuracy or damage; The drill should be slightly smaller than the major diameter of the thread to allow for proper material displacement during tapping. Material type and hardness also influence drill size selection, as harder materials may require specialized drills. Always consult the UNC chart or manufacturer guidelines to determine the optimal drill size for your application, ensuring accurate and durable thread production.
Support Pads for Thread Cutting
Support pads are essential for maintaining stability and preventing damage during thread cutting. The UNC thread chart recommends specific support pads based on thread size and material type. Proper pad selection ensures even pressure distribution, minimizing the risk of thread deformation or tool damage. The chart provides a reference for matching pads to thread specifications, ensuring precise alignment and consistent results. Material hardness and thread depth also influence pad choice, as softer materials may require thicker pads for stability. Always consult the UNC chart to select the correct support pad for your application, ensuring accurate thread cutting and extending tool life.
Material Considerations
Material selection is critical for UNC threads, with steel and aluminum being common choices. Plastics and composites are also used, requiring specialized cutting tools and techniques.
Steel and Aluminum Applications
Steel and aluminum are widely used for UNC threads due to their strength, durability, and versatility. Steel is preferred for high-load applications, while aluminum offers lightweight solutions. Both materials are easily machined, making them ideal for manufacturing. The UNC thread chart provides specific guidelines for threading these materials, ensuring precise dimensions and compatibility. In automotive and aerospace industries, these materials are commonly used for bolts, screws, and fasteners. Proper machining techniques, such as CNC cutting, ensure thread accuracy. Adherence to ANSI B1.1 standards guarantees consistency and reliability in final products, making steel and aluminum indispensable in modern engineering.
Plastics and Composites
Plastics and composites are increasingly used for UNC threads in lightweight applications. ANSI B1.1 provides guidelines for threading these materials, ensuring proper dimensions and strength. Plastics like nylon and polycarbonate are favored for corrosion resistance and ease of machining. Composites, such as carbon fiber reinforced polymers, offer high strength-to-weight ratios. Thread dimensions must be carefully adjusted to prevent material damage. Specialized taps and dies are often required for these materials. The UNC thread chart helps engineers select suitable thread sizes and pitches for plastic and composite components, ensuring durability and performance in applications like consumer goods and medical devices. Proper techniques ensure consistency with ANSI standards.
Specialized Materials for UNC Threads
Specialized materials like high-temperature alloys, stainless steel, and titanium are often used for UNC threads in demanding environments. These materials offer superior strength, corrosion resistance, and durability. The UNC thread chart includes specifications for threading these materials, ensuring proper dimensions and tolerances. High-temperature alloys, such as Inconel, are ideal for aerospace and industrial applications where extreme heat is present. Titanium, known for its strength-to-weight ratio, is commonly used in aerospace and medical devices. Exotic materials like tungsten or ceramic are also threaded using UNC standards for specific industrial applications. The chart provides guidance on thread dimensions and allowable tolerances, ensuring compatibility and performance in critical systems.
Quality Standards and Certification
UNC threads must comply with ANSI B1.1 and ISO standards, ensuring precision and reliability. Certification involves rigorous testing of thread dimensions, tolerances, and surface finish, guaranteeing compliance with industry benchmarks for safety and performance across various applications.
ANSI B1.1 Compliance
ANSI B1.1 establishes standardized specifications for UNC threads, ensuring dimensional consistency and interchangeability. Compliance requires adherence to defined nominal diameters, threads per inch, major diameters, and pitch dimensions. These standards guarantee reliable performance in mechanical assemblies. Manufacturers must verify thread accuracy through precise measurements, ensuring tolerances align with ANSI B1.1 guidelines. This compliance is critical for maintaining compatibility across different manufacturers and applications, reducing errors, and enhancing overall product reliability. Proper certification involves rigorous testing of thread dimensions, surface finish, and functional requirements, ensuring adherence to industry benchmarks for safety and performance.
ISO Standards for Thread Quality
ISO standards provide international guidelines for thread quality, complementing UNC specifications. These standards define parameters like thread form, pitch, and tolerance classes, ensuring global compatibility. ISO 261 specifies metric screw threads, while ISO 965-1 focuses on limits and fits. For UNC threads, ISO 1502 outlines gauge requirements, ensuring measurement accuracy. Compliance with ISO standards involves testing thread dimensions, surface finish, and functional requirements. These standards promote consistency across industries, enabling seamless integration of components worldwide. By adhering to ISO guidelines, manufacturers ensure high-quality products that meet global market demands, enhancing reliability and interoperability in diverse engineering applications.
Inspection and Testing Methods
Inspecting UNC threads involves precise measurements to ensure compliance with ANSI B1.1 and ISO standards. Thread gauges are commonly used to verify major and minor diameters, while the three-wire method measures pitch diameter accurately. Surface finish is evaluated to prevent roughness that could affect assembly or sealing. Functional testing includes checking thread angle, lead, and pitch to ensure proper mating. Advanced tools like optical scanners provide detailed thread profiles. These methods ensure threads meet specified tolerances and functional requirements. Regular inspection prevents defects, ensuring reliable performance in critical applications. Proper testing protocols are essential for maintaining quality and consistency in UNC threaded components.
Practical Tips for Using UNC Charts
Always cross-reference nominal diameters and threads per inch for accuracy. Use compatible tools like taps and dies for precise thread cutting. Regularly update charts for latest standards.
Matching Threads to Applications
Matching UNC threads to specific applications ensures optimal performance and durability. For instance, in automotive settings, coarse threads are often preferred due to their strength and resistance to vibration. In contrast, finer threads may be more suitable for aerospace applications where weight reduction and precision are critical. Industrial machinery often requires threads that balance strength and ease of assembly. By referring to the UNC thread chart, engineers can identify the appropriate thread specifications for their specific use case, ensuring compatibility and functionality. Proper matching also helps prevent issues like stripped threads or loose connections, enhancing overall product reliability.
Avoiding Common Mistakes
When using UNC thread charts, common mistakes include misidentifying thread specifications or using incorrect tools. Always verify the nominal diameter and threads per inch to ensure compatibility. Incorrect tap or die selection can lead to damaged threads or assembly issues. Additionally, neglecting to account for tolerances and allowances can result in non-compliant fasteners. Properly aligning the workpiece and using appropriate cutting oils can prevent thread distortion. Referencing the UNC chart meticulously helps minimize errors and ensures precise thread cutting. Regular inspection of tools and materials further enhances accuracy and quality in the final product.
Best Practices for Thread Cutting
For accurate UNC thread cutting, ensure precise alignment of the workpiece and tooling. Use high-quality taps and dies specifically designed for UNC threads. Always refer to the UNC chart for correct drill sizes and thread dimensions. Properly secure the material to prevent movement during cutting. Apply appropriate cutting oils to reduce friction and prevent tool wear. Maintain consistent cutting speeds and feeds to ensure thread integrity. Regularly inspect tools for wear and replace them as needed to avoid defective threads. Following these practices ensures high-quality, compliant UNC threads that meet ANSI B1.1 standards and perform reliably in their intended applications.
The UNC thread chart is a vital resource for precise fastener specifications. Adhering to ANSI B1.1 ensures reliability. As engineering evolves, UNC standards will continue to adapt, maintaining their critical role in manufacturing and design.
The UNC thread chart provides standardized specifications for fastener dimensions, ensuring compatibility and precision. It includes nominal diameters, threads per inch, major diameters, and pitch dimensions. Adhering to ANSI B1.1, the chart serves as a critical reference for manufacturers and engineers. Proper use of the chart prevents errors in thread cutting and ensures assembly reliability. By following the guidelines, professionals can maintain consistency across applications. The chart’s detailed measurements and tolerances are essential for achieving accurate results in various industries, from automotive to aerospace. Understanding and applying these standards is crucial for optimizing design and manufacturing processes.
Future Trends in Thread Standards
The future of UNC thread standards is expected to evolve with advancements in materials and manufacturing technologies. Increased demand for lightweight and high-performance materials will drive innovations in thread design. The integration of digital tools and automation in thread cutting processes will enhance precision and efficiency. Additionally, there will be a focus on sustainability, with standards adapting to eco-friendly materials and practices. As industries like aerospace and automotive continue to advance, UNC thread standards will likely incorporate new dimensions and tolerances to meet specialized requirements. These trends will ensure that UNC threads remain a cornerstone of engineering and manufacturing for years to come.