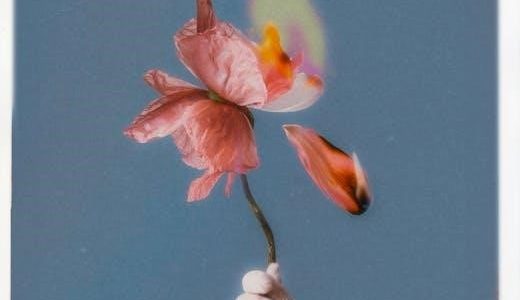
sublimation heat guide
Sublimation heat guide is essential for achieving vibrant, full-color transfers on various materials․ It ensures precise temperature, time, and pressure settings for optimal results in sublimation printing․
What is Sublimation Printing?
Sublimation printing is a cutting-edge technique that transfers vibrant, full-color designs onto materials using heat․ It involves a chemical process where solid sublimation ink turns directly into gas when heated, infusing into the substrate․ This method is ideal for fabrics, ceramics, metals, and other materials with a polymer coating․ Unlike traditional printing, sublimation creates durable, photo-quality images that won’t fade or crack․ It’s widely used in custom apparel, home decor, and promotional products due to its ability to produce intricate designs with minimal equipment․ The process requires precise temperature and pressure settings to ensure optimal results, making it a popular choice for creative and commercial applications․
Importance of Heat in Sublimation
Heat is the cornerstone of sublimation printing, activating the transition of solid sublimation ink into gas, which then infuses into the substrate․ Proper temperature ensures vibrant, durable transfers, while incorrect heat can cause ink to not transfer or damage materials․ The ideal range is typically 350-400°F, depending on the substrate․ Insufficient heat may result in faint images, while excessive heat can burn or discolor materials․ Balancing temperature with time and pressure is critical for achieving professional-quality results․ A sublimation heat guide provides precise settings to optimize transfers, ensuring consistent and high-quality outcomes across various materials like fabric, metal, and ceramics․ Heat control is key to mastering sublimation․
Key Factors Influencing Sublimation Results
Multiple factors significantly influence sublimation results․ Temperature is crucial as it must be high enough to convert ink into gas but not so high that it damages the material․ Pressing time must be precisely set to ensure the ink fully infuses without overdoing it․ Pressure should be even and adequate to maintain contact but not compress the substrate too much․ The substrate type and its coating play a big role in how well the ink adheres․ Environmental factors like humidity can affect the process, especially with certain materials․ The quality of sublimation paper and ink also matters for vibrant transfers․ Additionally, the thickness and texture of the substrate can impact heat distribution and transfer quality․ These factors often vary between materials and machines, making a heat guide essential for achieving consistent results․
Essential Equipment for Sublimation
A sublimation printer, heat press, and sublimation paper are the core tools needed․ A computer with design software and heat-resistant pads are also necessary for smooth operations․
Sublimation Printer and Ink
A sublimation printer is a vital tool, using sublimation ink to print designs onto transfer paper․ These printers are typically modified to handle sublimation dyes, ensuring vibrant color reproduction․ Epson models, like the EcoTank series, are popular for their reliability and compatibility with sublimation ink․ The ink transforms into gas during the heat press process, embedding colors into materials․ Always use high-quality, compatible ink to avoid print issues․ Proper printer calibration and regular maintenance are essential for consistent results․ The choice of printer and ink directly impacts the quality of the final sublimation transfer, making them foundational to the process․
Heat Press Machine
A heat press machine is a cornerstone of the sublimation process, applying heat and pressure to transfer designs onto materials․ It ensures the sublimation ink transforms into gas and bonds with the substrate․ Press machines vary in size and type, with clamshell, swing-away, and drawer models being common․ Temperature settings typically range from 350-400°F, while press time varies between 30-90 seconds, depending on the material․ Proper pressure adjustments are crucial to avoid damage or uneven transfers․ Using Teflon paper is recommended to prevent ink spillage and ensure a clean transfer․ The machine’s accuracy and durability directly impact the quality of sublimation results, making it an essential investment for consistent success․
Sublimation Paper
Sublimation paper is a specialized medium designed to work seamlessly with sublimation printers and inks․ It ensures vibrant and precise transfers of designs onto various substrates․ The paper is coated with chemicals that release the ink when exposed to heat, allowing it to sublimate into the material․ Compatibility with the printer and substrate is crucial for optimal results․ Always use paper specifically designed for sublimation, as it withstands high temperatures without degrading․ Proper placement, with the design face down, is essential for a successful transfer․ Additionally, using Teflon paper during pressing helps prevent ink spillage and ensures a clean, professional finish․
Temperature and Pressure Settings
Temperature and pressure settings are critical for successful sublimation transfers․ The ideal temperature range is typically between 350°F and 400°F (177°C to 204°C), with press times varying from 60 to 90 seconds depending on the material․ Pressure should be set to medium to high levels, around 40 PSI, to ensure proper contact between the paper and substrate․ Incorrect settings can lead to under-transfer or damage to the material․ Always use Teflon paper to prevent ink spillage and ensure a smooth process․ Adjustments may be needed based on the substrate and equipment used․ Follow manufacturer guidelines for specific materials to achieve the best results․
Sublimation Heat Press Settings by Material
Different materials require specific heat press settings for optimal sublimation results․ Adjust temperature, time, and pressure based on the substrate to ensure vibrant, durable designs․
Fabric
Fabric sublimation requires precise heat settings to ensure vibrant, long-lasting results․ Recommended temperatures range from 350°F to 400°F (177°C to 204°C), with press times of 30 to 45 seconds․ Medium pressure is ideal, as excessive pressure can damage the fabric or cause ink spillage; For polyester fabrics, a heat press mat is suggested to ensure even heat distribution․ Teflon paper should be placed on both sides to prevent ink from adhering to the press․ Pre-washing fabric before sublimation is advised to remove any finishes that might interfere with the process․ Proper cooling and immediate removal of the transfer paper are crucial for optimal results․ Adjust settings based on fabric thickness and weave for the best outcome․
Ceramics and Glass
For ceramics and glass, sublimation heat settings typically range from 350°F to 400°F (177°C to 204°C) with a press time of 60 to 90 seconds․ Medium to high pressure is recommended to ensure proper ink transfer․ The substrate must be clean and free of any protective coatings to achieve clear results․ Using Teflon paper is crucial to prevent ink spillage and ensure a smooth transfer․ Allow the substrate to cool slightly before handling, as sudden temperature changes can cause cracking․ Always pre-test a small area to ensure compatibility and desired outcomes․ Adjustments may be needed based on the specific ceramic or glass type being used․ Proper cooling and immediate removal of the transfer paper are essential for a flawless finish․
Metal Surfaces
Metal surfaces are a popular choice for sublimation due to their sleek, shiny finish and ability to retain intricate details․ For optimal results, set your heat press to 400°F (200°C) with a press time of 60-80 seconds at medium pressure (around 40 psi)․ Ensure the metal surface is clean and free of any protective coatings before pressing․ Using Teflon paper is highly recommended to prevent ink spillage and ensure a smooth transfer․ Remove the transfer paper immediately after pressing and allow the metal to cool slightly to prevent warping or damage․ These settings ensure vibrant, long-lasting designs on metal substrates, making them ideal for personalized gifts and decorative items․
Acrylic
Acrylic is a versatile material for sublimation, offering bright, durable transfers․ Set your heat press to 375°F (190°C) with a press time of 60 seconds at high pressure (around 40 PSI)․ Ensure the acrylic surface is clean and free of any plastic coatings before pressing․ Using Teflon paper is recommended to prevent ink spillage and protect the press․ Remove the transfer paper immediately after pressing for the best results․ These settings ensure vibrant, long-lasting designs on acrylic substrates, making them ideal for decorative items and personalized gifts․ Proper preparation and adherence to these guidelines are key to achieving professional-quality transfers․
MDF and Wood
Sublimation on MDF and wood requires precise settings for optimal results․ Set your heat press to 350-400°F (177-204°C) with a press time of 60-90 seconds at medium pressure․ Ensure the MDF or wood surface is coated and free of moisture for best results․ Using Teflon paper is recommended to prevent ink spillage and protect the press․ Allow the material to cool slightly before handling․ These settings ensure vibrant, durable transfers on wooden substrates, ideal for custom signs, plaques, and decorative items․ Proper preparation of the surface is crucial for achieving professional-quality sublimation results on MDF and wood․
General Guidelines for Sublimation Heat Transfer
Ensure optimal sublimation results by following key guidelines: use compatible materials, maintain recommended temperature and time settings, and apply consistent pressure for vibrant, durable transfers․
Temperature Range
The ideal temperature range for sublimation heat transfer typically falls between 300°F to 420°F (149°C to 220°C), depending on the material․ For fabrics, a range of 350°F to 400°F (177°C to 204°C) is common, while metals and ceramics may require higher temperatures․ It’s crucial to adjust the temperature based on the substrate’s thickness and coating․ Using a heat guide or chart can help determine the precise settings for specific materials․ Always preheat the press and ensure the substrate reaches the desired temperature for consistent results․ Monitoring temperature is key to achieving vibrant, durable transfers without damaging the material or causing ink spillage․
Press Time
Press time in sublimation varies depending on the material and the heat press’s power․ For most fabrics, a press time of 30-45 seconds is sufficient, while ceramics and glass typically require 60-90 seconds․ Metals usually need 60-80 seconds, and acrylics may take slightly less․ It’s important to allow the substrate to cool slightly before handling․ Over-pressing can lead to ink spillage or damage to the material, so adhering to the recommended time guidelines is crucial for achieving sharp, vibrant transfers․ Always refer to the specific heat guide for your material to ensure optimal results․
Pressure Settings
Pressure settings play a crucial role in sublimation heat transfer․ The ideal pressure ensures proper contact between the substrate and the transfer paper․ For most materials, medium to high pressure (around 30-40 PSI) is recommended․ Fabrics typically require light to medium pressure, while harder surfaces like ceramics or metal need higher pressure to ensure the design adheres evenly․ Using a heat press mat can help distribute pressure uniformly․ Incorrect pressure settings can lead to issues like uneven transfers or substrate damage․ Always refer to the material-specific guidelines to adjust pressure accurately for the best results․
Use of Teflon Paper
Teflon paper is a critical tool in sublimation heat transfer, protecting both the substrate and the heat press from ink spillage․ It ensures smooth, even transfers by preventing direct contact between the transfer paper and the press․ Place Teflon paper on both sides of the material for optimal results, especially with high-temperature substrates․ This prevents ink from seeping onto the press and extends its lifespan․ Always use high-quality Teflon sheets designed for sublimation to avoid melting or leaving residues․ Proper placement and replacement of Teflon paper after each use are essential for maintaining consistent, professional-quality transfers․
Troubleshooting Common Issues
Common sublimation issues like ghosting, press lines, and uneven transfers can be resolved by adjusting temperature, pressure, or time settings․ Proper Teflon paper use also helps prevent ink spillage․
Ghosting and Press Lines
Ghosting and press lines are common issues in sublimation, often caused by improper temperature or pressure settings․ Ghosting occurs when the design appears faint or blurry, while press lines are noticeable marks left by the heat press․ To address these, ensure even pressure distribution and adjust temperature settings within the recommended range for your material․ Using a Teflon sheet can help prevent press lines and ink spillage․ Additionally, avoid overloading the press and ensure the substrate is flat before pressing․ Proper alignment of the design and substrate is also crucial to avoid ghosting․ Adjusting press time and ensuring the heat press is preheated evenly can further minimize these issues․ Always refer to your sublimation heat guide for specific adjustments based on the material type․ Regular maintenance of the heat press and using high-quality sublimation paper also play a role in achieving flawless transfers․ By carefully monitoring these factors, you can significantly reduce the occurrence of ghosting and press lines in your sublimation projects․ Consistent results require attention to detail and adherence to optimal settings․
Ink Spillage
Ink spillage during sublimation can occur due to excessive ink flow or improper heat press settings․ To prevent this, use a Teflon sheet to protect the press and substrate․ Ensure the sublimation paper is compatible with your printer and ink․ High temperatures or prolonged press times can cause ink to spread unevenly․ Clean the heat press regularly to avoid ink buildup․ Proper alignment of the design and substrate is crucial to minimize spillage․ Adjusting the pressure settings to avoid over-compression can also help․ Using a heat-resistant pad or absorbent sheet beneath the substrate can catch excess ink․ Regularly maintaining the printer and heat press ensures consistent results and reduces the risk of ink spillage․ Always refer to your sublimation heat guide for material-specific recommendations to achieve clean, professional transfers․
Uneven Transfers
Uneven transfers in sublimation can occur due to inconsistent pressure, improper alignment, or uneven substrate surfaces․ Ensure the heat press applies uniform pressure across the material․ Check for any wrinkles or air pockets in the sublimation paper, as these can cause incomplete transfers․ Using a high-quality heat-resistant tape to secure the transfer paper can help maintain proper contact․ Environmental factors like humidity or uneven heating elements in the press may also contribute․ Preheating the substrate before pressing can improve consistency․ Always use a Teflon sheet to protect the substrate and ensure even heat distribution․ Adjusting the press time and temperature according to the material’s thickness and type can also help achieve more uniform results․ Regularly calibrating the heat press ensures consistent performance, minimizing the risk of uneven transfers․ Maintaining a clean and stable workspace further enhances the quality of sublimation outcomes․
Safety and Best Practices
Ensure proper ventilation and wear protective gloves when handling sublimation materials․ Always unplug the heat press when not in use and avoid overheating substrates․ Maintain a clean workspace and follow manufacturer guidelines for optimal safety and results in sublimation projects․
Heat Press Safety Tips
- Always operate the heat press in a well-ventilated area to prevent inhalation of fumes․
- Wear heat-resistant gloves to protect hands from burns during transfers․
- Never leave the heat press unattended while it is in operation․
- Ensure the press is placed on a stable, heat-resistant surface․
- Keep children and pets away from the heat press while in use․
- Avoid overheating substrates, as this can cause damage or release harmful chemicals․
- Regularly inspect the heat press for worn-out parts and replace them promptly․
- Unplug the heat press when not in use to prevent accidents․
Post-Press Cooling
Proper cooling after sublimation is crucial for preventing damage to the substrate and ensuring a durable transfer․ Always allow the pressed material to cool completely before handling or storing․ This step prevents cracking, peeling, or fading of the design․ For best results, let the item cool naturally on a heat-resistant surface․ Avoid exposing it to direct sunlight or moisture during the cooling process․ Additionally, never stack freshly pressed items, as residual heat can cause damage․ Cooling time varies depending on the material but typically ranges from 10 to 30 minutes․ This practice ensures long-lasting, vibrant finishes․
Environmental Considerations
Environmental considerations are crucial in sublimation printing to ensure sustainable practices․ Use eco-friendly sublimation inks and recyclable transfer papers to minimize waste․ Opt for energy-efficient heat presses to reduce power consumption․ Properly dispose of leftover ink and paper to prevent environmental contamination․ Choose substrates made from recycled or biodegradable materials when possible․ Regularly maintain equipment to optimize energy use and reduce long-term environmental impact․ By adopting these eco-conscious practices, you can contribute to a greener future while producing high-quality sublimation results․
Advanced Techniques in Sublimation
Advanced sublimation techniques involve multi-color transfers, unique materials, and layering for complex designs․ These methods require precision and creativity to achieve professional, high-quality results consistently․
Multi-Color Transfers
Multi-color transfers in sublimation require precise alignment and vibrant inks to achieve seamless, intricate designs․ Proper temperature and pressure settings ensure colors blend without ghosting or distortion․ Using high-quality sublimation paper and printers is crucial for maintaining color accuracy․ Heat press settings should be optimized to prevent ink spillage and ensure even transfer․ Layering techniques can enhance depth and detail, while advanced software tools help in designing complex multi-color patterns․ Regular calibration of the heat press and printer ensures consistent results across various materials, making multi-color transfers a standout feature in sublimation printing projects․ This technique is ideal for creating visually striking designs on fabrics, ceramics, and metal surfaces․ By mastering multi-color transfers, creators can unlock endless possibilities for custom products with professional-grade aesthetics․ Proper cooling and post-press care further enhance the durability and vibrancy of the transferred design․ Multi-color transfers are a key element in advancing sublimation technology for both hobbyists and professionals, offering a wide range of creative opportunities․ With the right equipment and techniques, multi-color sublimation transfers can elevate any project to new heights, ensuring vivid and long-lasting results․
Sublimation on Unique Materials
Sublimation on unique materials like MDF, wood, and acrylic offers creative possibilities for custom projects․ For MDF and wood, lower temperatures (375°F/190°C) and longer press times (60-90 seconds) are recommended to avoid burning․ Acrylic requires high pressure (40 PSI) at 375°F for 60 seconds, with immediate transfer paper removal․ Always ensure materials are coated or treated for sublimation to achieve vibrant transfers․ Proper surface preparation, such as sanding or removing plastic coatings, is essential for optimal results․ These unique substrates expand the range of sublimation applications, allowing for innovative designs on unconventional surfaces․ Experimenting with settings and materials can unlock new creative opportunities for crafters and businesses alike․
Layering and Overprinting
Layering and overprinting in sublimation enable the creation of intricate, multi-color designs․ This technique involves applying multiple layers of ink to achieve vibrant, detailed transfers․ For layering, align each layer carefully and use lower temperatures (300-350°F) to prevent ghosting․ Overprinting allows for full-color overlays without smudging, ensuring crisp results․ Proper pressure (40 PSI) and time (60-90 seconds) are crucial for even fusion․ These advanced methods expand creative possibilities for complex designs on fabrics, ceramics, and other materials․ Experimenting with layering and overprinting can enhance the visual appeal of sublimation projects, making them stand out in both personal and commercial applications․ Always test settings on small areas first to ensure optimal results․
Future Trends in Sublimation Technology
Advancements in heat press precision and eco-friendly inks are expected to dominate sublimation trends, alongside innovative substrates and smarter temperature control systems for enhanced efficiency and sustainability․
Improvements in Heat Press Machines
Future heat press machines are expected to feature enhanced precision, automation, and smarter controls․ Advanced models may include touchscreen interfaces, Wi-Fi connectivity, and real-time monitoring apps for optimal sublimation results․ Improved heat distribution systems will ensure uniform transfers across various materials, reducing ghosting and press lines․ Energy-efficient designs with faster heating elements and eco-friendly components are also anticipated․ These advancements aim to simplify the sublimation process, minimize production time, and cater to both small-scale and industrial applications, making high-quality sublimation more accessible and sustainable for creators and businesses alike․
Innovative Substrates
The development of innovative substrates is expanding the possibilities for sublimation printing․ New materials like eco-friendly plastics, recycled fabrics, and advanced ceramics are being introduced, offering sustainable and durable options․ Researchers are also exploring substrates with unique properties, such as self-healing surfaces or adaptive textures, which can enhance the visual appeal of sublimated designs․ Additionally, the use of 3D-printed substrates is becoming popular, allowing for intricate shapes and custom geometries that were previously impossible to achieve․ These advancements are making sublimation more versatile and environmentally responsible, opening up new creative avenues for designers and businesses․
Eco-Friendly Sublimation Practices
Eco-friendly sublimation practices focus on reducing environmental impact while maintaining high-quality results․ Using recyclable or biodegradable sublimation paper and ink is a key step․ Many manufacturers now offer eco-conscious alternatives that minimize waste and chemical emissions․ Additionally, optimizing heat press settings to use less energy without compromising output is a sustainable approach․ Recycling leftover materials and properly disposing of hazardous waste also play a crucial role․ By adopting these practices, businesses can align with environmental standards while producing vibrant, durable designs․ Eco-friendly substrates, such as organic fabrics or sustainable ceramics, further enhance the green appeal of sublimation projects․