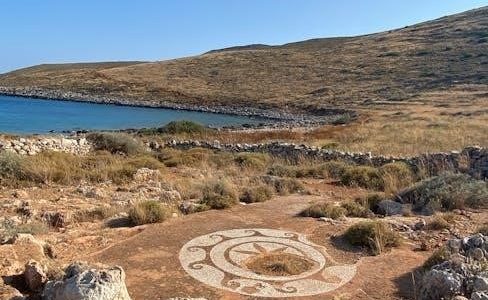
plasma cutter circle guide
Cutting perfect circles with a plasma cutter can be challenging, especially for beginners. This guide provides essential tips, techniques, and tools to achieve precise, smooth cuts. Learn how to overcome common issues and master circular cuts with ease.
Why Circle Cutting Matters in Metal Fabrication
Circle cutting is a fundamental skill in metal fabrication, essential for creating precise holes, curves, and circular patterns. Achieving smooth, accurate cuts is crucial for professional results and structural integrity. Whether fabricating pipes, tanks, or decorative designs, circular cuts are often required. A plasma cutter circle guide enhances efficiency, allowing for consistent and precise cuts, which is vital for maintaining quality and reducing material waste; This technique is particularly valuable in industries like automotive, construction, and art, where intricate designs and functional components demand accuracy. By mastering circle cutting, fabricators can improve project outcomes, meet client expectations, and streamline their workflow. It is a skill that combines artistry with technical precision, making it indispensable in modern metalworking.
What is a Plasma Cutter Circle Guide?
A plasma cutter circle guide is a specialized tool designed to assist in cutting precise circular shapes with a plasma cutter. It typically consists of a compass-like mechanism that attaches to the plasma torch, allowing for smooth, consistent cuts around a central point. This tool is particularly useful for fabricators who need to create accurate holes or circular patterns in metal sheets or plates. By maintaining consistent distance and alignment, the guide minimizes errors and improves the quality of the cut. It is an essential accessory for both manual and CNC plasma cutting setups, enabling users to achieve professional-grade results with ease. The guide is especially beneficial for intricate designs and projects requiring multiple identical circles, ensuring precision and consistency.
Selecting the Right Plasma Cutter for Circle Cutting
Selecting the right plasma cutter for circle cutting involves considering power, duty cycle, and precision. Choose a model with adjustable settings for accurate, smooth cuts.
Factors to Consider When Choosing a Plasma Cutter
When selecting a plasma cutter for circle cutting, consider several key factors. Power output is crucial, as higher amperage allows for thicker metal cutting. Duty cycle determines how long the cutter can operate without overheating, essential for continuous cuts. Precision and control are vital for accurate circles, so look for models with adjustable speed and fine-tuned settings. Compatibility with your workspace, such as air supply requirements and electrical needs, is also important. Additionally, budget and durability should be evaluated to ensure the cutter meets your long-term needs. These factors combined will help you find the ideal plasma cutter for your projects.
Recommended Plasma Cutters for Precise Circle Cutting
For precise circle cutting, the Spectrum 875 stands out as a top choice, offering high power and accuracy for thick metals. The Dynatorch 5×10 is another excellent option, known for its CNC compatibility and smooth operation. Beginners may prefer the CUT-50 plasma cutter, which is affordable and user-friendly. The Vipercut 30i is also recommended for its versatility and performance on various steel thicknesses. These models are highly rated for their ability to produce clean, accurate cuts, making them ideal for both manual and CNC plasma cutting tasks. Each offers unique features suited to different skill levels and project requirements, ensuring optimal results in metal fabrication.
Setting Up Your Workspace for Effective Circle Cutting
A well-organized workspace is crucial for precise plasma cutting. Ensure a stable surface, proper ventilation, and use guides or jigs for accurate circle cuts.
Optimizing Your Workspace Layout
Organizing your workspace efficiently is key to achieving precise plasma cuts. Start by ensuring your worktable is sturdy and level to prevent any uneven cuts. Keep your plasma cutter and accessories within easy reach to minimize distractions. Use magnetic circle guides or jigs to help maintain accuracy, especially for intricate cuts. Proper ventilation is essential to avoid inhaling harmful fumes, so invest in a good exhaust system. Consider using a crosshair or laser guide to align your cutter accurately. Finally, ensure good lighting to clearly see your workpiece and cutting path. A well-organized workspace not only enhances precision but also improves safety and efficiency during your projects.
Safety Tips for Plasma Cutter Operations
Safety is paramount when working with plasma cutters. Always wear protective gear, including heat-resistant gloves, safety glasses with a shade #5 lens, and a face shield to protect against sparks and UV radiation. Ensure proper ventilation in your workspace to avoid inhaling toxic fumes. Keep a fire extinguisher nearby, as plasma cutting generates high temperatures and sparks. Avoid wearing loose clothing or jewelry that could catch fire or get caught in equipment. Ensure the workpiece is securely clamped to prevent movement during cutting. Never touch the plasma torch or workpiece with bare hands, as they can be extremely hot. Regularly inspect the plasma cutter and its consumables for damage or wear. Ground the equipment properly to prevent electrical shocks; By following these safety guidelines, you can minimize risks and ensure a safe cutting experience.
Techniques for Cutting Perfect Circles
Mastering circle cutting requires precision and control. Use guides or templates for manual cuts, and ensure proper software settings for CNC operations. Maintain consistent speed and arc stability to achieve smooth, accurate results.
Manual Plasma Cutter Techniques for Circle Cutting
Cutting perfect circles manually with a plasma cutter requires skill and patience. Start by using a guide or template to maintain consistency. Ensure the torch remains perpendicular to the workpiece to avoid uneven cuts. Maintain arc stability by keeping the standoff consistent and adjusting the cutting speed as needed. For smaller circles, reduce your travel speed to prevent lag, while larger circles may require slightly higher speeds. Practice on scrap metal to refine your technique, as muscle memory plays a significant role in manual cutting. Use a steady, smooth motion, and avoid applying too much pressure, which can cause the torch to deviate from the path. Regularly inspect your consumables to ensure optimal performance. With practice, manual circle cutting can yield professional-grade results.
CNC Plasma Cutter Techniques for Accurate Circles
For precise circle cutting, CNC plasma cutters offer superior accuracy and consistency. Ensure your machine is properly calibrated and free from flex, especially when cutting small circles. Use G-code optimized for circular paths, and enable radius compensation to maintain exact geometries. Maintain consistent arc voltage and adjust the cutting speed based on material thickness. Utilize a high-quality circle cutting guide or compass for manual adjustments. Regularly inspect and replace consumables to prevent irregularities. Implementing these techniques ensures smooth, accurate cuts every time, making CNC plasma cutting ideal for intricate designs and repetitive tasks. Proper setup and maintenance are key to achieving professional-grade results consistently.
Troubleshooting Common Issues in Circle Cutting
Address uneven cuts and precision loss by checking plasma cutter settings, consumable condition, and material alignment. Ensure proper arc stability and torch positioning for smooth, accurate results.
Addressing Uneven Cuts and Lack of Precision
Uneven cuts and precision issues often stem from improper plasma cutter setup or worn consumables. Ensure the torch is perpendicular to the workpiece and the nozzle is clean. Check the arc voltage and adjust settings for consistent power. Regularly inspect and replace worn electrodes and nozzles, as they can cause irregular cuts. Proper material alignment and secure clamping are crucial to prevent movement during cutting. Additionally, maintaining the correct stand-off distance ensures a stable arc, which is vital for precise results. By addressing these factors, you can significantly improve the quality and accuracy of your circle cuts for professional-grade finishes.
Maintaining Arc Stability for Smooth Cuts
A stable arc is crucial for smooth, even cuts when using a plasma cutter. To maintain arc stability, ensure the torch is held at the correct angle and distance from the material. Clean and inspect the consumables regularly, as debris or wear can disrupt the arc. Proper airflow and consistent power settings also play a key role in arc stability. Avoid overheating the torch by allowing it to cool between cuts. Additionally, use a high-quality plasma cutter with good arc control features. By following these practices, you can achieve consistent, smooth cuts and extend the life of your equipment for optimal performance.
Maintenance and Care for Your Plasma Cutter
Regular cleaning, inspecting consumables, and proper storage are essential for maintaining your plasma cutter. Ensure all components are in good condition to guarantee optimal performance and longevity.
Regular Maintenance to Ensure Optimal Performance
Regular maintenance is crucial for your plasma cutter’s efficiency and longevity. Start by cleaning the torch and nozzle daily, removing any debris or metal particles that may accumulate. Inspect the consumables, such as the electrode and nozzle, for wear and tear, replacing them when necessary. Check the air filter and compressor for moisture and dust, ensuring clean, dry air flows through the system. Lubricate moving parts and ensure all connections are secure. Perform a test cut periodically to assess performance. Proper storage in a dry, cool place prevents rust and damage. Adhering to these steps ensures consistent, high-quality cuts and extends the life of your plasma cutter.
Proper Care of Plasma Cutter Consumables
Proper care of plasma cutter consumables is essential for maintaining performance and extending their lifespan. Regularly clean the nozzle, electrode, and shield using compressed air to remove metal particles and debris. Store consumables in a dry, cool place to prevent rust and corrosion. Avoid touching the nozzle or electrode with bare hands, as oils from skin can damage the components. Inspect consumables after each use for signs of wear, such as erosion or discoloration, and replace them when necessary. Properly align and tighten consumables to ensure optimal arc stability. Clean or replace the air filter in the compressor to maintain clean, dry air flow. By following these care tips, you can ensure consistent cutting results and reduce replacement costs.
Mastering plasma cutter circle cutting requires practice, patience, and proper techniques. Apply the strategies learned, maintain your tools, and explore more complex projects. For further growth, seek tutorials, forums, and hands-on workshops to refine your skills and stay updated on the latest methods and technologies.
Summarizing Key Takeaways
Effective plasma cutter circle cutting involves selecting the right tools, mastering manual and CNC techniques, and ensuring proper machine maintenance. Use circle cutting guides or compass tools for precision, especially for thick metals. Regularly inspect and replace consumables to maintain cut quality. Optimize workspace layout for efficiency and safety, ensuring proper ventilation and fire precautions. Troubleshoot issues like uneven cuts by checking arc stability and material thickness. Practice consistent techniques, whether manual or CNC, to achieve smooth, accurate results. Always refine your skills through experimentation and learning from common challenges. By following these guidelines, you can confidently cut precise circles and expand your metal fabrication capabilities.
Encouragement to Apply Learned Techniques
Now that you’ve learned the essential techniques for cutting perfect circles with a plasma cutter, it’s time to put them into practice; Start with small projects to build confidence and refine your skills. Experiment with different materials and sizes to see how your techniques adapt. Remember, practice is key to achieving consistent results. Don’t be discouraged by initial challenges—each cut brings you closer to mastery. As you progress, you’ll notice improvements in precision and efficiency. Apply these methods to real-world projects, whether crafting decorative pieces or fabricating functional components. With patience and dedication, you’ll unlock the full potential of your plasma cutter and create stunning, professional-quality circular cuts. Keep experimenting, learning, and pushing your creative boundaries in metal fabrication.
Additional Resources for Further Learning
To deepen your understanding of plasma cutter circle cutting, explore additional resources like tutorials, videos, and forums. Websites such as YouTube and specialized metalworking forums offer hands-on demonstrations and tips. Books on metal fabrication and plasma cutting provide detailed insights and troubleshooting guides. Online courses and workshops can also enhance your skills, offering structured learning paths. Many plasma cutter manufacturers provide user manuals and guides specific to their models, which can be invaluable for optimizing performance. Additionally, communities like Reddit’s r/metalworking and r/plasmacutting share experiences and solutions from experienced fabricators. By leveraging these resources, you can refine your techniques, stay updated on best practices, and explore advanced methods for achieving perfect circular cuts.