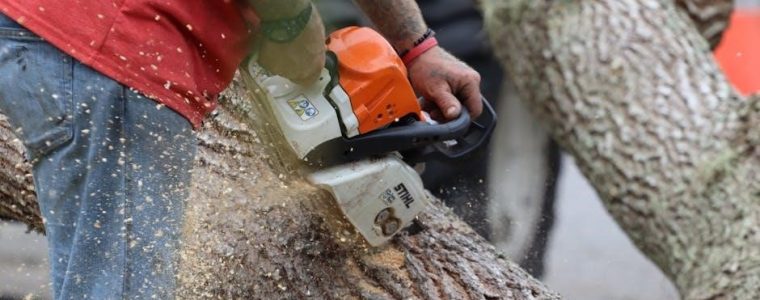
manual handling risk assessment sample
A manual handling risk assessment is a systematic process to identify and evaluate tasks involving manual handling that could pose risks of injury to workers․
1․1 What is Manual Handling?
Manual handling refers to any task that involves lifting, lowering, pushing, pulling, carrying, or holding objects, which can pose risks to employees’ health and safety․
1․2 Importance of Manual Handling Risk Assessment
Conducting a manual handling risk assessment is crucial to identify and control risks associated with manual handling tasks, reducing the likelihood of injuries․ It helps employers ensure compliance with legal requirements and promotes a safer working environment․ By evaluating tasks, employers can implement appropriate control measures, protecting employees from musculoskeletal disorders․ Regular assessments also foster awareness and accountability, leading to improved workplace safety and efficiency․
Key Components of a Manual Handling Risk Assessment
A manual handling risk assessment involves identifying tasks, evaluating risks, and recording findings․ It ensures a systematic approach to managing hazards, protecting workers from injury․
2․1 Identifying Manual Handling Tasks
Identifying manual handling tasks involves recognizing activities that require lifting, pushing, pulling, or carrying․ These tasks often involve repetitive motions or awkward postures․ Employers should observe workplace operations to pinpoint tasks that may pose risks․ For example, lifting heavy objects or maneuvering bulky loads are common manual handling tasks․ Additionally, tasks that involve sustained awkward positions or high frequencies of movement should be identified․ By systematically reviewing workplace activities, employers can effectively pinpoint tasks that require further assessment to ensure worker safety and compliance with regulations․
2․2 Assessing the Risks
Assessing the risks involves evaluating the likelihood and potential severity of injury from manual handling tasks․ This includes analyzing task demands, load characteristics, and environmental factors․ The MAC (Manual Handling Assessment Chart) tool is often used to quantify risks․ Additionally, factors such as the weight, size, and stability of the load, as well as the worker’s physical capabilities, are considered․ A thorough risk assessment helps identify high-risk tasks and informs the implementation of effective control measures to reduce the likelihood of injury․
2․3 Recording the Assessment
Recording the assessment ensures documentation of identified risks, control measures, and outcomes․ Templates and checklists are commonly used to detail tasks, risk levels, and actions taken․ This documentation serves as a reference for compliance, future reviews, and employee training․ Accurate records help track progress and verify that risks have been adequately managed․ Employers must maintain these records to demonstrate compliance with legal requirements and to ensure continuity in managing manual handling risks effectively over time․
The Process of Conducting a Manual Handling Risk Assessment
The process involves identifying tasks, assessing risks, implementing controls, and monitoring outcomes to ensure a safe working environment and compliance with legal requirements effectively․
3․1 Step 1: Identify the Task
The first step involves recognizing specific manual handling tasks within the workplace․ This includes activities like lifting, carrying, pushing, or pulling objects․ Employers must observe and list all tasks that involve manual handling to ensure comprehensive risk identification․ By clearly defining each task, the assessment process becomes more targeted and effective, allowing for precise evaluation of potential hazards․ This step lays the foundation for subsequent risk analysis and control implementation, ensuring a systematic approach to workplace safety․
3․2 Step 2: Assess the Risks
After identifying the task, the next step is to assess the risks associated with it․ This involves evaluating factors such as the weight of the load, posture required, distance of movement, and environmental conditions․ Using tools like the MAC (Manual Handling Assessment Chart) or other techniques, employers can determine the level of risk and identify potential harm to workers․ This step ensures that all hazards are considered, allowing for informed decision-making to reduce or eliminate risks effectively․ A thorough assessment is critical for safeguarding employee health and preventing injuries․
3․3 Step 3: Implement Controls
Once risks are identified, the next step is to implement controls to reduce or eliminate them․ This can include engineering controls, such as introducing mechanical aids or redesigning the task to minimize manual effort․ Administrative controls, like adjusting work patterns or providing training, are also effective․ Personal Protective Equipment (PPE) may be necessary in some cases․ Employers should involve employees in selecting and implementing controls to ensure practicality and acceptance․ Regular monitoring is essential to assess the effectiveness of these measures and make adjustments as needed to maintain a safe working environment․
3․4 Step 4: Monitor and Review
Monitoring and reviewing are crucial to ensure the effectiveness of implemented controls․ Regular checks should be conducted to assess whether the risks have been adequately managed․ Feedback from employees is invaluable, as they can provide insights into the practicality of the controls․ Reviews should also be triggered by any changes in the task, workforce, or workplace conditions․ Updates to the risk assessment should be documented and communicated to all relevant parties․ This step ensures ongoing safety and adaptability in the workplace․
Tools and Techniques for Manual Handling Risk Assessment
Tools like the MAC (Manual Handling Assessment Chart) and checklists are widely used to evaluate manual handling risks․ These tools help identify and prioritize hazards effectively․
4․1 The MAC (Manual Handling Assessment Chart) Tool
The MAC Tool is a widely recognized method for assessing manual handling risks․ It evaluates factors like weight, distance, frequency, and posture to determine the risk level․ By analyzing these elements, the tool helps identify tasks that may cause injury․ Employers can use MAC to prioritize controls and reduce workplace hazards effectively․ This approach ensures a systematic and thorough evaluation of manual handling tasks, promoting a safer working environment for employees․
4․2 Other Assessment Techniques
Besides the MAC Tool, other techniques include checklists, ergonomic evaluations, and observational studies․ Checklists help identify hazards in manual handling tasks, while ergonomic assessments focus on posture and workplace layout․ Observational studies allow real-time analysis of worker movements, providing insights into potential risks․ Additionally, task-specific assessments can be tailored to unique work environments, ensuring comprehensive risk evaluation․ These methods complement the MAC Tool, offering employers a versatile approach to managing manual handling risks effectively in various workplace settings․
Common Manual Handling Risk Assessment Templates
Templates simplify the risk assessment process by providing structured forms to identify and evaluate manual handling tasks systematically․
5․1 Generic Manual Handling Risk Assessment Template
A generic manual handling risk assessment template provides a standardized framework to evaluate tasks involving manual handling across various industries․ It typically includes sections for task description, risk factors such as load weight and posture, and existing control measures․ The template also allows for assessing risk levels and identifying actions to mitigate hazards․ By using a generic template, organizations can ensure consistency in their risk assessment process and compliance with regulatory requirements․ It is often tailored to specific workplace environments and tasks․
5․2 Task-Specific Manual Handling Risk Assessment Template
A task-specific manual handling risk assessment template is tailored to evaluate risks associated with particular manual handling tasks, such as lifting, pushing, or carrying․ It includes detailed sections for task description, frequency, and duration, as well as specific risk factors like posture, load weight, and distance carried․ This template allows for a focused assessment of hazards unique to the task, enabling targeted control measures to reduce injury risks․ It is particularly useful for high-risk or repetitive tasks, ensuring a thorough evaluation of workplace-specific conditions․
Examples of Manual Handling Risk Assessments
Examples include assessments for lifting, carrying, and pushing tasks, demonstrating how to identify hazards and implement control measures to reduce injury risks effectively․
6․1 Example 1: Lifting and Carrying
An example of a manual handling risk assessment for lifting and carrying involves evaluating tasks like moving heavy boxes․ Assessors consider factors such as the weight of the load, the distance carried, and the posture of the worker․ Risks like muscle strain or injury from awkward lifting are identified․ Control measures may include reducing the load weight, providing handling aids, or training employees in proper lifting techniques to minimize the risk of harm and ensure a safer working environment․
6․2 Example 2: Pushing and Pulling
An example of a manual handling risk assessment for pushing and pulling involves tasks like moving heavy carts or trolleys․ Key factors include the force required, the distance pushed or pulled, and the surface conditions․ Risks such as shoulder or back strain are common due to excessive force or poor postures․ Control measures may involve adjusting handle heights, using assistive equipment, or redesigning workflows to reduce the physical demands․ Proper training in techniques can also minimize injury risks in these tasks․
Reducing the Risks of Manual Handling
Reducing manual handling risks involves ergonomic adjustments, mechanical aids, and proper training․ Regular risk assessments and employee feedback further enhance safety measures effectively․
7․1 Engineering Controls
Engineering controls are physical modifications or equipment designed to reduce manual handling risks․ Examples include mechanical lifting aids, adjustable workstations, and automated systems․ These solutions minimize physical strain by eliminating or reducing the need for manual force․ Employers often implement ergonomic tools, such as hoists or conveyor belts, to redistribute the workload․ Properly designed equipment can significantly lower the risk of musculoskeletal injuries, ensuring a safer working environment․ Regular maintenance of these systems is essential to maintain their effectiveness․
7․2 Administrative Controls
Administrative controls focus on managing workflows and policies to minimize manual handling risks․ These include implementing safe work practices, training programs, and job rotation schedules․ Employers can reduce risk by limiting task duration and frequency, ensuring adequate rest breaks, and providing clear guidance on proper techniques․ Supervision and monitoring of manual handling tasks also fall under administrative controls․ These measures aim to reduce the physical demands of tasks and promote a safer working environment without relying solely on physical modifications․
7․3 Personal Protective Equipment (PPE)
Personal Protective Equipment (PPE) plays a crucial role in reducing manual handling risks․ Gloves can prevent cuts and abrasions, while back supports help maintain proper posture and reduce strain․ Anti-slip footwear minimizes the risk of accidents during pushing or pulling tasks․ PPE should be selected based on the specific risks of the task and ensure a proper fit․ Employers must train workers on the correct use and maintenance of PPE to maximize its effectiveness in protecting against manual handling injuries․
7․4 Training and Awareness
Effective training and awareness programs are essential for reducing manual handling risks․ Employees should receive comprehensive instruction on proper lifting techniques, hazard identification, and the use of PPE․ Regular updates and refresher courses ensure ongoing understanding․ Employers must foster a culture of safety, encouraging workers to report unsafe practices and participate in risk assessments․ Practical demonstrations and hands-on training further enhance employees’ ability to perform tasks safely, minimizing injury risks and promoting a proactive approach to workplace safety․
Legal and Regulatory Requirements
Employers must comply with legal standards, such as the Manual Handling Operations Regulations 1992, to minimize risks and ensure worker safety through proper assessments and controls․
8․1 Relevant Legislation
Key legislation governing manual handling includes the Manual Handling Operations Regulations 1992 and the Health and Safety at Work Act 1974․ These laws require employers to assess and reduce risks associated with manual handling tasks․ The MAC (Manual Handling Assessment Chart) tool, provided by the HSE, helps employers evaluate tasks systematically․ Non-compliance can result in legal consequences, emphasizing the importance of adhering to these regulations to ensure workplace safety and protect employees from injuries related to manual handling activities․
8․2 Compliance and Enforcement
Compliance with manual handling regulations is enforced by the Health and Safety Executive (HSE), which conducts workplace inspections and investigates incidents․ Employers must demonstrate adherence to the Manual Handling Operations Regulations 1992 by implementing risk assessments and control measures․ Failure to comply can result in fines, legal action, and reputational damage․ Regular audits and employee feedback help ensure ongoing compliance․ Employers are also required to maintain records of risk assessments and control measures implemented to mitigate manual handling risks in the workplace․
Best Practices for Manual Handling Risk Assessment
Best practices involve continuous improvement, employee collaboration, and regular updates․ Utilize tools like the MAC tool, ensure compliance, and maintain detailed records for accountability․
9․1 Involving Employees in the Assessment Process
Involving employees enhances the accuracy of manual handling risk assessments․ They provide insights into task-specific challenges and suggest practical controls, fostering a safety-focused culture․ Encourage feedback and participation in identifying risks and implementing solutions․ This collaborative approach ensures assessments are comprehensive and relevant, leading to more effective risk mitigation strategies․ Regular training and open communication channels further empower employees to contribute meaningfully to the process․
9․2 Regular Review and Update of Assessments
Regularly reviewing and updating manual handling risk assessments ensures they remain relevant and effective․ Workplace changes, new equipment, or updated tasks may require revisions․ Reviews should occur periodically or when significant changes occur․ This process helps identify new risks and ensures existing controls remain adequate․ Keeping assessments up-to-date promotes a safer work environment and compliance with legal requirements․ It also demonstrates a proactive approach to managing health and safety risks associated with manual handling tasks․
Manual handling risk assessments are essential for identifying and mitigating risks associated with manual handling tasks․ By systematically evaluating tasks, employers can implement effective controls to reduce injuries․ Regular reviews ensure assessments remain relevant, while tools like the MAC tool provide structured approaches․ Compliance with legal requirements and fostering a safer work environment are key outcomes․ Ultimately, a well-managed manual handling risk assessment process promotes worker well-being and operational efficiency, ensuring continuous improvement in workplace safety standards․