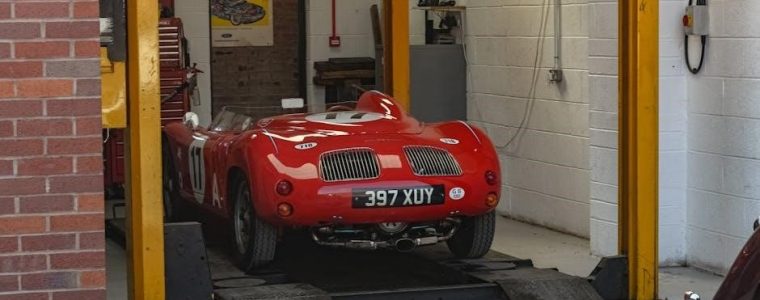
delta variable frequency drive manual
A Delta Variable Frequency Drive (VFD) is an advanced motor control device enabling efficient speed regulation․ Designed for applications requiring precise torque and power management, models like VFD-B and VFD-F enhance operational efficiency and energy savings across various industries․
1․1 Overview of VFD Technology
Variable Frequency Drive (VFD) technology is a motor control system that adjusts the frequency and voltage supplied to an AC motor to regulate its speed․ This technology enables precise control over motor operation, optimizing performance for various applications․ By converting AC power to DC and then back to AC at adjustable frequencies, VFDs provide smooth speed adjustments․ They are widely used in industries like manufacturing, HVAC, and automation to improve energy efficiency and reduce mechanical stress on motors․ Models such as the VFD-B and VFD-F series are designed for reliability and versatility, offering features like remote control via RJ11 connectors and advanced parameter settings․ Proper installation, including correct motor cable lengths and grounding, is crucial for safe and efficient operation․ This technology ensures reduced energy consumption and extended motor lifespan․
Variable Frequency Drives (VFDs) are essential for modern motor control, offering unparalleled flexibility and efficiency․ By adjusting speed dynamically, VFDs optimize energy usage, reducing consumption by up to 50% in some applications․ This directly lowers operational costs and environmental impact․ Additionally, VFDs minimize mechanical stress on motors during startup, extending equipment lifespan․ They also enable precise control for applications requiring variable speed, such as pumps, fans, and conveyors․ With features like remote operation via RJ11 connectors and advanced parameter settings, VFDs enhance system automation and scalability․ Proper installation, including correct motor cable lengths and grounding, ensures safe and reliable operation․ Moreover, VFDs reduce harmonic distortion, improving overall power quality․ Their versatility and benefits make them indispensable in industries like manufacturing, HVAC, and automation․ By integrating VFD technology, industries achieve higher efficiency, reduced downtime, and long-term cost savings․ This ensures sustainable and reliable motor control across diverse applications․ The Delta VFD comprises power circuit components like IGBTs and capacitors, control circuit elements including microprocessors, and HMI options like keypads for user interaction․ These components ensure efficient motor control and protection, with features like RJ11 connectors for remote operation and advanced grounding methods to prevent damage․ Proper installation and parameter settings are crucial for optimal performance․ The VFD also includes safety features to protect against overcurrent and voltage fluctuations, ensuring reliable operation across various industrial applications․ Regular maintenance, such as checking motor cables and insulation, is essential to prevent damage and extend lifespan․ By integrating these components, the Delta VFD provides precise speed control, energy efficiency, and system flexibility․ This design ensures compliance with safety standards and environmental regulations, making it a robust solution for modern motor systems․ The VFD’s modular design allows for easy configuration and scalability, catering to diverse industrial needs while maintaining high performance and reliability․ The inclusion of diagnostic tools and alarm monitoring further enhances operational efficiency and troubleshooting capabilities, ensuring minimal downtime and maximized productivity․ Overall, the Delta VFD’s advanced components and features make it a key asset in achieving efficient and sustainable motor control solutions․ The Delta VFD’s power circuit includes essential components like IGBTs (Insulated Gate Bipolar Transistors), capacitors, and rectifiers; These elements work together to convert AC input to DC and then to variable frequency AC output․ The IGBTs act as high-speed switches, enabling precise control over motor speed and torque․ Capacitors are used for filtering and storing energy, ensuring stable DC voltage․ The rectifier converts AC input to DC, which is then inverted back to AC by the IGBTs․ Proper grounding and voltage ratings are critical, with 240V models requiring specific connections to avoid damage․ The power circuit also includes protective features like overcurrent and voltage surge protections․ These components ensure efficient energy conversion, reduce harmonic distortion, and provide reliable operation․ Regular inspection of motor cables and insulation is recommended to prevent damage from voltage spikes․ By integrating these advanced power components, the Delta VFD delivers high performance and energy efficiency in motor control applications․ The control circuit of the Delta VFD includes microprocessors, keypad interfaces, and communication modules․ These components enable precise control and monitoring of motor operations․ The microprocessor acts as the central processing unit, executing control algorithms and managing input/output signals․ Keypad interfaces allow users to set parameters, monitor status, and adjust settings․ Communication modules like RS-485 enable integration with external systems․ The control circuit also includes sensors for monitoring voltage, current, and temperature․ Overvoltage and under-voltage protections are integrated to safeguard the drive․ Proper grounding and wiring are essential to avoid interference and ensure reliable operation․ The control circuit works seamlessly with the power circuit to optimize motor performance, provide real-time feedback, and support advanced control strategies․ Additionally, the control circuit supports firmware updates, ensuring the drive remains up-to-date with the latest features and improvements․ This integration of advanced electronics ensures high reliability and flexibility in motor control applications․ The Delta VFD offers a range of Human-Machine Interface (HMI) options for intuitive operation and monitoring․ A built-in keypad allows users to adjust settings, monitor motor speed, and start/stop the drive․ For enhanced functionality, an online keypad can be connected via an RJ11 connector, enabling remote control and parameter adjustments․ Additionally, Delta VFDs support graphical LCD displays for real-time visualization of operational data, including speed, torque, and alarm status․ These interfaces provide a user-friendly way to interact with the drive, ensuring precise control and easy troubleshooting․ The HMI options are designed to simplify operation, making it accessible for both novice and experienced users․ By integrating these features, the Delta VFD enhances operational efficiency and adaptability across various industrial applications․ These interfaces are also customizable to meet specific application requirements, ensuring a tailored user experience․ The HMI options are a key feature of the Delta VFD, contributing to its versatility and ease of use․ Proper installation ensures safe and efficient operation․ Use an RJ11 connector for online keypad models․ Ensure grounding complies with local laws․ Inspect the drive for damage and use correct cables to avoid damage․ Always disconnect AC power before wiring․ Before installing the Delta VFD, perform thorough checks to ensure compatibility and safety․ Inspect the drive for any damage during transportation․ Verify the rated voltage matches the motor specifications, such as 240V for 230V models․ Check the motor cable length to avoid insulation damage; use a frequency inverter-duty cable if the distance is long․ Ensure the grounding method complies with local regulations․ Review the Basic Wiring Diagram for correct connections․ Never reconnect internal components or wiring․ Disconnect AC power before any wiring to prevent charges․ Ensure the correct model is selected for the application (e․g․, VFD-F series for specific regulations)․ These steps ensure safe and efficient operation of the Delta VFD․ Mount the Delta VFD in a well-ventilated area to ensure proper cooling․ Avoid direct exposure to sunlight or moisture․ Use the provided mounting brackets to secure the drive firmly․ For wiring, refer to the Basic Wiring Diagram to avoid incorrect connections․ Use an RJ11 connector for models like VFD-B and VFD-F․ Ensure all cables are tightly connected to prevent loose terminals․ Before wiring, disconnect the AC power source to avoid potential charges in the drive․ Never reconnect internal components or wiring․ Use a frequency inverter-duty cable for long motor connections to protect insulation․ Double-check the wiring configuration to match the motor and power specifications․ Proper wiring ensures safe and efficient operation of the Delta VFD, preventing damage and improving system reliability․ Always follow the manufacturer’s guidelines for optimal performance․ Proper grounding is essential for the safe operation of the Delta VFD․ Ensure the grounding method complies with local electrical regulations and standards․ Use a grounding wire to connect the drive’s chassis to a reliable earth point․ Before installation, inspect the drive for any damage during transportation․ Disconnect the AC power supply before performing any wiring or maintenance tasks․ Avoid using incorrect cables, as this can cause irreversible damage to the drive․ For models like VFD-B and VFD-F, ensure the rated voltage matches the input power specifications․ Never reconnect internal components or wiring, as this can lead to system failure․ Always follow the manufacturer’s safety guidelines to prevent electrical hazards․ Proper grounding and adherence to safety precautions ensure the longevity and reliable operation of the Delta VFD․ Regular checks and compliance with regulatory standards are crucial for maintaining a safe working environment․1․2 Importance of Variable Frequency Drives in Motor Control
Key Components of the Delta VFD
2․1 Power Circuit Components
2․2 Control Circuit Components
2․3 Human-Machine Interface (HMI) Options
Installation Guidelines
3․1 Pre-Installation Checks
3․2 Mounting and Wiring Recommendations
3․3 Grounding Methods and Safety Precautions
Configuration and Parameter Settings
Configure Delta VFDs using the keypad or software for precise motor control․ Set basic parameters like motor speed and torque․ Adjust advanced settings for optimized performance and energy efficiency․
4․1 Basic Parameter Settings for Motor Control
Begin by setting the rated voltage and frequency of the motor to ensure compatibility with the VFD․ Select the motor’s rated current and power to optimize performance․ Configure the maximum and minimum frequency to match the application’s speed requirements․ Set the acceleration and deceleration times to prevent mechanical stress․ Enable the appropriate motor control mode, such as V/F or vector control, depending on the motor type․ Adjust the starting torque to ensure smooth motor startup․ Finally, verify all settings with the motor manufacturer’s specifications to ensure safe and efficient operation․
4․2 Advanced Parameter Configuration
Advanced parameter settings allow customization of the VFD for specific applications․ Adjust the torque boost to improve starting performance under heavy loads․ Enable slip compensation for precise speed control in variable-load scenarios․ Configure the PID control parameters for accurate process regulation․ Set custom acceleration and deceleration curves to match machine requirements․ Adjust frequency limits to optimize energy efficiency․ Enable advanced features like energy-saving mode to reduce power consumption․ Configure harmonics reduction settings to comply with power quality standards․ Set up feedback control using encoder or tachometer inputs for high-precision speed regulation․ Define custom alarms and notifications for critical operating conditions․ Adjust the DC bus voltage regulation to stabilize power supply․ Enable remote monitoring and control via communication interfaces like Modbus or Ethernet; Ensure all settings align with the motor and load characteristics for optimal performance and reliability․
4․3 Using the Keypad or Software for Setup
Configuring the Delta VFD can be done via the integrated keypad or specialized software․ Start by connecting the keypad using an RJ11 connector, compatible with models like VFD-B and VFD-F․ Power on the drive and navigate through the menu to access basic settings․ Adjust parameters such as motor speed (Hz) and voltage to match your motor specifications․ For advanced customization, use Delta’s software, downloadable from their official website․ Connect the VFD to your computer via USB or RS485, ensuring proper communication․ The software offers features like custom alarms, real-time monitoring, and precise control․ Use the keypad to start/stop the drive and adjust speed manually․ Ensure all wiring meets safety standards, including the use of frequency inverter duty cables to prevent motor damage․ Regularly update the software for the latest features and security patches․ Always refer to the user manual for specific guidance tailored to your VFD model․
Operation and Control
Operate the Delta VFD by first disconnecting AC input power before wiring․ Use the RJ11 connector for models like VFD-B and VFD-F․ Start/stop the drive and adjust motor speed using the keypad or software․ Always monitor drive status and ensure proper grounding to prevent damage․ Refer to the manual for detailed operation guidance․
5․1 Starting and Stopping the Drive
To safely start and stop the Delta VFD, ensure all pre-operation checks are completed․ Disconnect AC input power before performing any wiring․ Use the RJ11 connector for models like VFD-B and VFD-F․ Begin by powering up the drive and ensuring no alarms are present․ Start the motor using the keypad or software interface, gradually increasing speed as needed․ For stopping, reduce the motor speed to zero before disconnecting power․ Always follow the recommended sequence to prevent sudden stops or damage․ Regular inspections, such as checking for transportation damage and proper motor cable installation, are crucial for smooth operation․ Refer to the manual for specific start/stop procedures and safety guidelines to ensure optimal performance and longevity of the drive․
5․2 Adjusting Motor Speed
Adjusting motor speed with a Delta VFD is achieved through the keypad or software interface․ Ensure the motor cable length is appropriate to prevent insulation damage; use a frequency inverter duty cable if necessary․ Start by setting the desired frequency using the keypad, then gradually increase or decrease the speed as needed․ The VFD allows precise control, enabling smooth acceleration and deceleration․ Always monitor the motor’s performance to avoid overloading․ For models like VFD-B and VFD-F, refer to the manual for specific parameter settings․ Adjustments should be made while the motor is running to ensure accurate control․ Regularly inspect the motor and drive for optimal performance․ Remember to disconnect power before making any wiring changes to ensure safety and avoid damage to the system․
5․3 Monitoring Drive Status and Alarms
Monitoring the Delta VFD’s status and alarms is essential for maintaining optimal performance․ Regularly inspect the drive for damage during transportation or installation․ Use the keypad or software interface to review operational status and alarm history․ Common alarms include overvoltage, undervoltage, and overheating․ Address these issues promptly to prevent damage․ For models like VFD-B and VFD-F, ensure the rated voltage matches the motor specifications․ Refer to the manual for specific alarm codes and troubleshooting steps․ Always disconnect power before performing inspections or repairs․ Grounding must comply with local regulations to prevent system damage․ Use the basic wiring diagram for guidance․ Proper monitoring ensures reliable operation and extends the lifespan of the drive․
Maintenance and Troubleshooting
Regular maintenance ensures optimal performance․ Inspect for damage, check cables, and ensure proper grounding․ Disconnect power before wiring․ Avoid internal component reassembly to prevent irreversible damage․ Refer to the manual for troubleshooting common issues like overvoltage or overheating․
6․1 Routine Maintenance Checks
Regular maintenance is crucial for ensuring the longevity and efficiency of a Delta VFD․ Begin by visually inspecting the unit for any signs of physical damage or wear․ Check the input and output cables for secure connections and ensure there are no loose wires․ Verify that the grounding method complies with local regulations, as improper grounding can lead to malfunctions or safety hazards․ Next, inspect the power components, including the capacitors and heat sinks, for any signs of degradation or overheating․ Clean any dust or debris from the unit to maintain proper airflow and cooling․ Additionally, review the motor cable length and ensure it is suitable to prevent insulation damage․ Regularly updating the firmware and software can also enhance performance and resolve potential issues․
6․2 Common Issues and Diagnostic Techniques
Common issues with Delta VFDs often relate to power supply, motor performance, or control functionality․ One frequent problem is improper grounding, which can cause malfunctions or safety risks․ To diagnose, ensure the grounding method complies with local regulations and verify the connections․ Another issue is motor noise or vibration, which may indicate incorrect motor cable length or improper installation․ Inspect the cable for damage and ensure it meets the recommended specifications․ Additionally, communication errors with the keypad or software can occur, requiring a check of settings and connections․ For power-related issues, ensure the input voltage matches the rated voltage of the VFD․ Always refer to the Basic Wiring Diagram for troubleshooting․ If the drive fails to start, check for damage during transportation or improper wiring․ Regular diagnostic checks can prevent these issues and ensure optimal performance․
6․3 Repair and Replacement Guidelines
For repair, always follow manufacturer-recommended procedures to avoid further damage․ Disconnect power before performing any internal repairs․ If the drive is damaged during transportation, inspect for visible defects and test functionality immediately․ Improper grounding or incorrect cable connections can lead to irreversible damage, so ensure all wiring matches the Basic Wiring Diagram․ Never reassemble internal components, as this can render the device inoperable․ If replacement is necessary, ensure the new unit matches the specifications of the original VFD․ Always use frequency inverter-duty motor cables to prevent insulation damage․ Rated voltage must align with the VFD model specifications to avoid malfunction․ Refer to regulatory standards for compliance during repairs․ Regular maintenance and diagnostic checks can prevent the need for extensive repairs․ If unsure, consult professional technicians to ensure safety and optimal performance․
Safety and Compliance
Always disconnect power before wiring or servicing․ Ensure proper grounding according to local regulations․ Use RJ11 connectors for VFD-B and VFD-F models․ Follow safety precautions to avoid damage during transportation or installation․ Comply with regional standards for safe operation and environmental considerations․ Refer to regulatory guidelines for rated voltage specifications and wiring requirements․ Proper grounding methods prevent damage and ensure compliance with safety standards․ Always use appropriate cables to maintain motor insulation integrity and avoid potential hazards․ Adhere to all safety protocols to ensure safe handling and installation of the Delta VFD․ Regulatory compliance is essential for safe and efficient operation․ Ensure all installations meet local and international safety standards․ Always follow manufacturer guidelines for safe handling and installation practices․ Proper grounding ensures safe operation and prevents damage․ Always use frequency inverter-duty cables to protect motor insulation․ Ensure rated voltage matches specifications for safe operation․ Follow all safety precautions to avoid risks during installation and operation․ Regulatory compliance ensures adherence to safety and environmental standards․ Always refer to the Basic Wiring Diagram for safe connections․ Proper grounding prevents damage and ensures compliance with safety regulations․ Use correct connectors like RJ11 for VFD-B and VFD-F models to maintain safety and functionality․ Always check for transportation damage before installation․ Ensure all wiring meets regional standards for safe operation․ Follow safety guidelines to prevent damage and ensure optimal performance․ Always disconnect power before servicing to avoid hazards․ Proper grounding and wiring ensure compliance with safety standards․ Use appropriate cables to protect motor insulation and maintain safety․ Adhere to regulatory standards for safe installation and operation․ Always follow manufacturer recommendations for safe handling and maintenance․ Proper grounding and wiring prevent damage and ensure compliance․ Use correct connectors and cables for safe and efficient operation․ Follow all safety precautions to avoid risks and ensure regulatory compliance․ Always refer to the manual for specific guidelines and recommendations․ Proper grounding and wiring ensure safe installation and operation․ Use appropriate cables and connectors to maintain safety and functionality․ Follow all safety protocols to prevent damage and ensure compliance․ Always check for damage before installation and ensure proper wiring․ Regulatory compliance ensures safe and efficient operation․ Always follow manufacturer guidelines for safe handling and installation․ Proper grounding prevents damage and ensures safe operation․ Use correct cables and connectors for optimal performance․ Follow all safety precautions to avoid risks and ensure compliance․ Always refer to the manual for specific instructions and recommendations․ Proper grounding and wiring ensure safe and efficient operation․ Use appropriate cables and connectors to maintain safety and functionality․ Follow all safety protocols to prevent damage and ensure regulatory compliance․ Always check for transportation damage and ensure proper installation․ Adhere to safety standards for safe handling and operation․ Always disconnect power before servicing to avoid hazards․ Proper grounding and wiring prevent damage and ensure compliance․ Use correct connectors and cables for safe operation․ Follow all safety guidelines to ensure optimal performance and regulatory compliance․ Always refer to the manual for specific instructions and recommendations․ Proper grounding and wiring ensure safe installation and operation․ Use appropriate cables and connectors to maintain safety and functionality․ Follow all safety precautions to avoid risks and ensure compliance․ Always check for damage before installation and ensure proper wiring․ Regulatory compliance ensures safe and efficient operation․ Always follow manufacturer guidelines for safe handling and installation․ Proper grounding prevents damage and ensures safe operation․ Use correct cables and connectors for optimal performance․ Follow all safety protocols to prevent damage and ensure compliance․ Always refer to the manual for specific guidelines and recommendations․
7․1 Safety Precautions for Handling and Installation
Always disconnect AC input power before performing any wiring or maintenance․ Ensure the drive is properly grounded according to local regulations to prevent damage․ Check for transportation damage before installation and avoid exposing the device to extreme environments․ Use frequency inverter-duty cables for motor connections to prevent insulation damage․ Never connect incorrect cables to input/output terminals, as this can cause irreversible damage․ Ensure the rated voltage matches the model specifications (e․g․, 240V for 230V models)․ Refer to the Basic Wiring Diagram for correct connections․ Avoid reassembling internal components or wiring, as this can lead to operational failure․ Always follow safety guidelines to prevent hazards during handling and installation․
7․2 Environmental Considerations
Delta VFDs are designed to operate in various environments, but proper conditions must be maintained for optimal performance․ Ensure the ambient temperature remains within the specified range (typically 0°C to 40°C) and humidity levels do not exceed 95% RH․ Avoid installing the drive in areas with high dust, corrosive substances, or excessive vibration․ For outdoor use, ensure the enclosure is IP-rated and suitable for the environment․ Proper ventilation is essential to prevent overheating․ The device should be stored in a clean, dry place before installation․ Environmental factors like electromagnetic interference (EMI) can be mitigated using shielded cables and proper grounding; Always follow local environmental regulations and guidelines for electrical equipment installation․ Adhering to these considerations ensures reliable operation and extends the lifespan of the VFD․
7․3 Regulatory Compliance and Standards
Delta VFDs are designed to meet global regulatory standards, ensuring safety and performance across different regions․ The drives comply with CE, UL, and RoHS certifications, adhering to international safety and environmental requirements․ Specific models, such as the VFD-B and VFD-F series, are engineered to satisfy regional regulations, including those related to electromagnetic compatibility (EMC)․ Always ensure the rated voltage matches the application, with 240V models designed for 230V systems․ Incorrect wiring or voltage mismatches can cause irreversible damage․ Grounding methods must comply with local electrical codes to prevent hazards․ Refer to the Basic Wiring Diagram for proper installation․ Regulatory compliance ensures the drive operates safely and efficiently, minimizing environmental impact․ Adherence to these standards is crucial for both performance and legal requirements, guaranteeing reliable operation and minimizing potential risks․